Mechanical CAD and manufacturing software are essential tools that enable professionals to design, analyze, simulate, and manufacture products with precision and efficiency. These tools have revolutionized the way products are designed and brought to market, reducing the time and cost associated with traditional manufacturing methods. Collaboration is a key element for these products, as users must be able to easily work on designs together in real-time, sometimes in different time zones. The technology continues to evolve, giving users more flexibility and options to design. CAD continues to push the boundaries so that the users can focus on design.
Time between design and production continues to decrease, making it easier for products to come to market quickly, and pushing designers to work quickly and efficiently.
What Users Need in Mechanical CAD and Manufacturing Software
Mechanical engineers and designers need software that is intuitive, offers advanced modelling capabilities, iterative options, and more. Needs include:
- Intuitive Design Interface: Users want easy-to-navigate user interfaces that facilitate the design process and are easy to understand.
- Advanced Modeling Capabilities: Tools for creating detailed 3D models and simulations, digital twins.
- Compatibility and Integration: Seamless integration with other software and compatibility with various file formats.
- Customization: Ability to customize tools and workflows to fit specific project needs.
- Collaboration Features: Tools that support team collaboration and data sharing, including cloud connectivity.
- Manufacturing Readiness: Features that prepare designs for manufacturing (DfAM), including CAM (Computer-Aided Manufacturing) capabilities and support for additive manufacturing (3D printing).
- Performance and Scalability: Software that can handle complex designs without compromising on performance, with scalability to match project demands.
- Sustainability. The consumer packaged goods industry is seeing a growing demand for eco-friendly packaging. This is forcing a change for manufacturing. Digital twin technology will assist the transition to sustainable packaging because the digital twin offers an accurate digital representation of the part or product.
- Artificial Intelligence (AI). AI will continue to develop within software products, helping make workflows more efficient and finishing repetitive tasks. AI implemented in MCAD software gives users ability to choose between multiple iterations and other tools such as this.
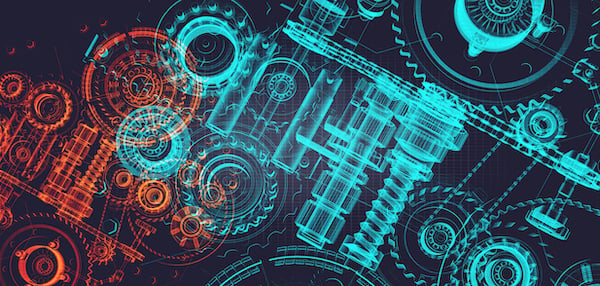
Image source: Photocreo Bednarek/stock.adobe.com.
Overview of Mechanical CAD and Manufacturing 3D Software Programs
There are numerous software product available; this is not an exhaustive list, but does give an overview of some 3D programs available.
AutoCAD
Developed by Autodesk, AutoCAD offers a robust set of tools for 2D and 3D design and drafting. Autodesk states that: AutoCAD equips architects, engineers, and construction professionals with precision tools to: Design and annotate 2D geometry and 3D models with solids, surfaces, and mesh objects; automate drafting tasks to place objects with AI, compare drawings, create schedules, publish layouts, and more; plus maximize productivity with customized workspaces, AutoLISP, APIs, and apps.
Find out more about AutoCAD 2025 here.
Dig into programming, by reading Cadalyst’s CAD Programming articles: Rediscovering AutoLISP and More Fun with AutoLISP.
Inventor
Also from Autodesk, Inventor is a 3D CAD software for mechanical design, documentation, and product simulation. It integrates with AutoCAD and other Autodesk software, providing a seamless workflow for product development. It offers a blend of parametric, direct, freeform, and rules-based design capabilities, plus integrates tools for sheet-metal design, frame design, tubes and piles, and more.
Fusion 360
Fusion 360 also from Autodesk combines CAD, CAM (computer-aided manufacturing), and CAE (computer-aided engineering) in a single platform, facilitating the design-to-manufacturing process. It supports cloud-based collaboration across the platform.
Creo
Creo (formerly known as Pro/ENGINEER) is a 3D model-based design program from PTC. It offers features for product design and manufacturing, including parametric and direct modeling, real-time simulation, and additive manufacturing capabilities. Creo is also available as a SaaS (software as a service) product.
CATIA
Dassault Systèmes’ CATIA (Computer-Aided Three-dimensional Interactive Application) is known for its engineering, design, and systems engineering capabilities, combining CAD, CAE, and CAM together. It is widely used in aerospace, automotive, and industrial machinery industries for complex product designs. It offers a variety of modules, such as part design, assembly design, drafting, and surfacing. CATIA also works with the 3DS 3DEXPERIENCE Platform bringing organizations into a real-time “single collaborative environment,” according to the company.
SOLIDWORKS
SOLIDWORKS, also from Dassault Systèmes, is a leading 3D CAD software designed for mechanical engineering, product design, and manufacturing. It is known for its interface, solid modeling, and simulation capabilities. SOLIDWORKS is now part of Dassault Systemes’ 3DS 3DExperience, the company’s cloud technology platform.
Find out about SolidWorks’ 2D offspring, DraftSight here.
Siemens NX
Siemens NX offers a suite of integrated tools for product engineering, including design, simulation, and manufacturing. It is known for its features and scalability, catering to industries such as aerospace, automotive, and machinery. Users chose from three packaged solutions that bundle the software to fit a team’s needs. NX X Design Standard offers ability to create and edit designs of typical 3D parts and assemblies. NX X Design Advanced offers an enhanced set of design capabilities and NX X Design Premium is the full set of design tools offered.
Solid Edge
Solid Edge, also from Siemens, combines the speed and simplicity of direct modeling with the flexibility and control of parametric design. Solid Edge is a portfolio of software tools for the whole product development process. It also offers simulation, manufacturing, and data management tools. The program is part of Siemens Xcelerator, the company’s portfolio of software, hardware, and services.
Online Programs
There are a variety of programs that are online-only.
TinkerCAD: TinkerCAD is a free, easy-to-use, web-based application for beginners to learn more about 3D design, electronics and coding. Developed by Autodesk, it focuses on building new designers’ excitement about design and teaching hands-on skills.
FreeCAD: FreeCAD is an open-source parametric 3D modeler suitable for adjusting designs by going back into the model history and changing its parameters. You can sketch geometry constrained 2D shapes and use them to design other objects. It is multiplatform and reads and writes a variety of file formats, such as STEP, IGES, STL, SVG, DXF, and more. In addition, it offers FEA (finite element analysis) tools, experimental CFD, BIM, geodata or CAM/CNC workbenches, a robot simulation module, and more.
Onshape: A cloud-based CAD system that allows for real-time collaboration, access from any device, and a built-in PDM (product data management) system. Designers, customers, and external partners can access, collaborate, and work concurrently from conception of a product to production. It offers built-in collaboration tools for communication within the program. The program’s customization tools, including FeatureScript is a programming language that allows users to create custom CAD tools. There is a free plan for personal projects, a Standard Plan ($1,500/year) for individual users, a Professional Plan ($2,500/year) for teams, and an Enterprise solution (call for more information).
Other Programs
Alibre Design
Altium Designer
Ansys
BricsCAD Mechanical
DesignCAD 3D Max
DesignSpark
KeyCreator
Mastercam
MATLAB
Mathcad
MechDesigner
nTopology
Simcenter
TurboCAD
VectorWorks
ZWCAD
Manufacturing Technology
Additive Manufacturing
The first 3D printers on the market quickly became known in manufacturing as “rapid prototyping” machines. Today they have become much more. 3D printing, now known as additive manufacturing (AM), is a concept introduced by Jon Hirschtick, the co-founder of SOLIDWORKS and Onshape, and is rapidly becoming accepted as the third primary method of industrial fabrication, along with formative and subtractive. For more about AM, read Cadalyst's series, "Additive Manufacturing 101."
One reason for the rapid growth of AM is that AM processes can sometimes accomplish what is otherwise impossible. For example, simulation software can confirm how oddly arranged channels improve cooling, yet such novel designs are either impossible to make with CNC or too expensive to make with formative methods. Enter AM, which can prove the design works.
Design for Additive Manufacturing (DfAM) is a merger of design and simulation and applying it to additive manufacturing. Where simulation-driven design is a methodology using specific software, DfAM is more an emphasis on intentions. To design with a goal of additive manufacturing is to focus on elements including manufacturability, functional performance, materials, reliability, and cost — all with an eye to the specific 3D printing method that will be used for production.
Artificial Intelligence in Manufacturing
Broadly speaking, AI algorithms in MCAD (and in simulation, factory design, and other related software) analyze data, recognize patterns, and use that information to make intelligent design decisions. Machine learning algorithms in MCAD allow software to adapt, optimize performance, and make predictions based on exposure within the scope of the design project. Already, many software programs are harnessing the power of AI to streamline simulation, optimize composite materials, and enhance overall design efficiency.
Generative Design
PTC defines generative design (GD) as: “a method of using AI algorithms to generate and evaluate multiple design alternatives based on input from the user. This design process can take many factors into account, including performance requirements, manufacturing processes, and materials to generate optimized designs.” GD with the help of AI brings speed and opportunities to designers' fingertips. In minutes or even seconds, programs can help useres discard or select the design that fits a variety of constraints.
Digital Twins for Manufacturing
In a recent article from Cadalyst, we delved into digital twins for manufacturing: Autodesk defines a digital twin for manufacturing as a virtual representation of a real-world product or asset “with the benefit of continuous, real-time data from the object.” The twin becomes both a reflective and real-time source of information “to help improve business practices, reduce downtime, and increase ROI.”
Discussions today about digital twin technology have it backwards. Some companies create a digital version after manufacturing, as a record. Or, they create a model for simulation, but don’t connect it to the physical device. Yet, for those who have made the leap to digital twins, the resulting feedback loop provides valuable data for both service operations and future design upgrades.
The majority of product engineering projects create three distinct bills of materials (BOMs), the engineering BOM, the manufacturing BOM, and the service BOM. If the product is a small engine, the engineering BOM can show the engine as a single unit, but the service BOM must show all the distinct parts. Such granularity can be used to generate both As Built and As Maintained models. Additionally, the service BOM as a digital twin can keep track of product use, serial numbers of replaced parts, and more. The goal is to have constantly updated information that a tech in the field can use.
This technology will continue to grow and become more powerful. The ability to use the designs through the life of a product and to use that information to better the design in its next iteration will push design success. In addition, the technology will become available across the board.
Conclusion
Mechanical CAD and manufacturing software are indispensable in the modern design and production landscape. From well-established giants like AutoCAD and SOLIDWORKS to emerging cloud-based platforms such as Onshape, these tools cater to a wide range of needs, offering solutions for every aspect of product development, from conceptualization to manufacturing. As technology advances, these programs continue to evolve, providing ever more powerful and efficient ways to bring innovative products to market that push the boundaries of what is possible.
______________________________
Note: This article pulls together a broad range of information from Cadalyst.com articles. Click on the linked topics for full discussion.